Numerical modelling of Aluminium electrolysis process
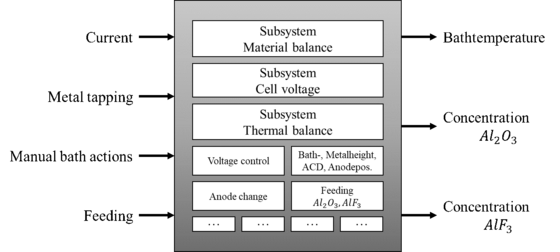
The production of aluminium is a very energy intensive process. Several research studies have been conducted to understand the complex process involving chemical reactions, heat transfer, influence of the electric field, magnetic field and the effect of thermal and mechanical stresses in components employed at the production. These studies have shown that there is still a lot of space for optimizing the process and improving the energy efficiency. Another factor which plays a major role in production is the fluctuating generation of renewable energy. Since its availability and consequently its price is continuously varying, it would be favourable to tap more energy from the grid when the prices are comparatively low and vice versa. This allows for a better and more efficient use of renewable energy resources. This modulation in the electrical energy requires that the heat balance in the electrolysis cell should also be maintained for undisturbed production of aluminium. An increase in electric current leads to increased heat generation in the cell. When the extra heat generated reaches a point where the molten electrolyte comes in direct contact with the Silicon carbide wall, it melts through the wall damaging the cell and halting the production process. Hence, the extra heat generated should be removed from the cell to ensure uninterrupted production of aluminium. When operating at lower electrical energy, the thickness of solid ledge formed around the wall starts to increase leading to inefficient aluminium production. Therefore, the aim of the project is to achieve flexibility and energy efficiency of the aluminium production.
Digital twin model
One step to achieve these goals is the development of a digital twin for numerical modelling of the aluminium electrolysis process. The present Simulink model can generally represent the Hall-Héroult process. It is specified for the common process configurations of the electrolytic cells of TRIMET Aluminium SE, the cooperative industrial partner in aluminium production. The digital twin will be mainly used to predict the bath temperature. On the one hand for variable current modulations, regarding the predicted energy costs and fluctuations. On the other hand, to reduce the need for laborious temperature measurements. The model contains a large number of process parameters. These are constantly measurable values or time-variable signals and some estimations or experience values.
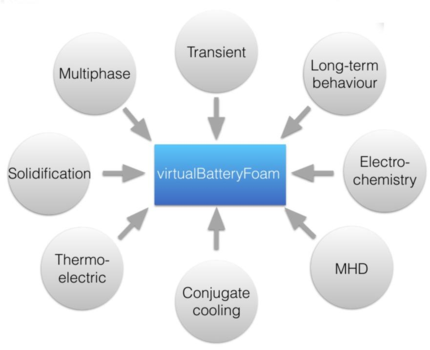
VirtualBatteryFOAM
To realize the aim of the project, it is necessary to have a deeper understanding of the different phenomena occurring in the production cell and the complicated inter dependencies between each other. Therefore, OpenFOAM®, an opensource CFD software, is employed in the project to model various physics like CHT, multiphase flows, solidification process and electrodynamics among others and a multiphysics library called virtualBatteryFOAM is being developed. These steps are also carried out in cooperation with the TRIMET Aluminium SE.

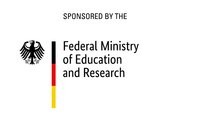
Research Projects
SynErgie II (in progress)
This research project is sponsored by the German ministry of education and research under the program "SynErgie - Synchronized and Energy adaptive Production Engineering for flexible Adjustment of Industrial Processes referring to fluctuating Energy Supply", which is a part of the "Industrial processes" Kopernikus projects for energy revolution.
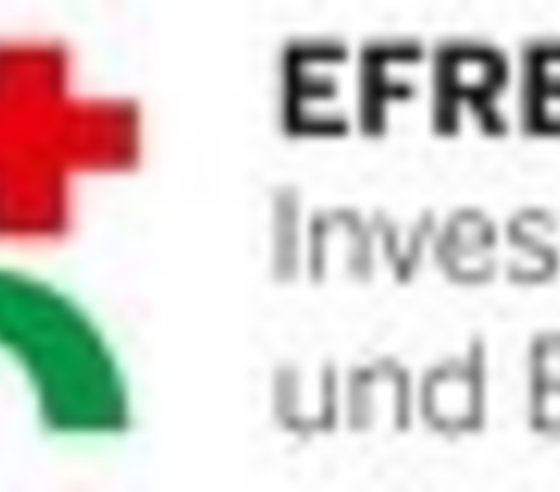
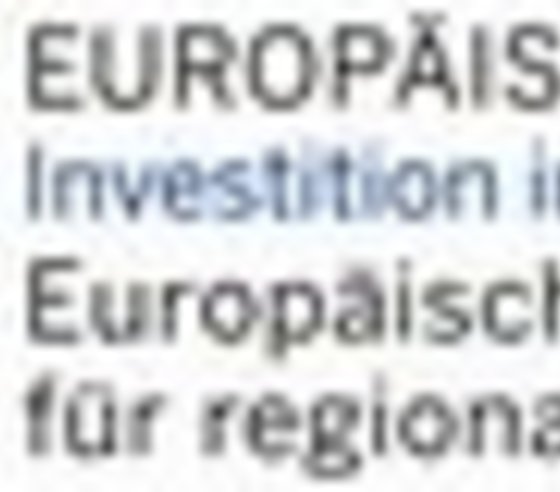
Aluminium Elektrolyse 4.0 (completed)
This research project is funded by the program "Europäischer Fonds für regionale Entwicklung (EFRE) 2014-2020 - Investitionen in Wachstum und Beschäftigung".
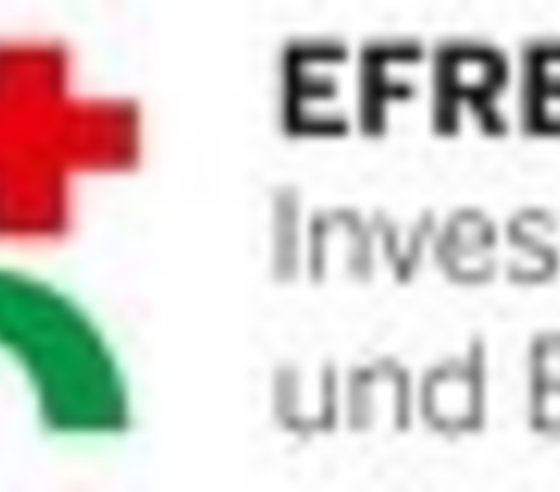
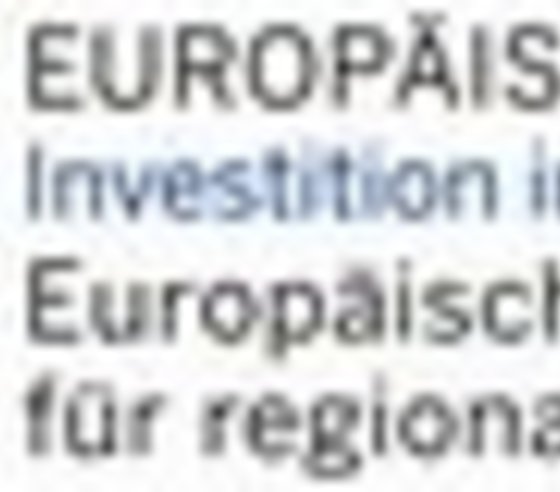
FlexTerm (completed)
This research project is funded by the program "Europäischer Fonds für regionale Entwicklung (EFRE) 2014-2020 - Investitionen in Wachstum und Beschäftigung".